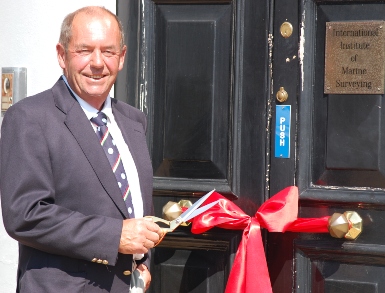
As the Institute has finally taken ownership in recent weeks of Murrills House as its new flagship headquarters, President, Geoff Waddington, arrived (pictured right) to perform the ribbon cutting duties and ceremony to officially mark the completion.
The work to restore this magnificent Grade II listed, 500-year-old building to its former glory will begin shortly. Completion on the deal took far longer than was anticipated, but the outcome marks something of a triumph for the Institute. IIMS is soon to make a significant financial investment in essential maintenance and repair work which will only add to the value of this new asset.
Discussions have taken place with a local construction firm and the scope of work has been drawn up and agreed. The building survey threw up some key maintenance work that needs to be done with a degree of urgency, but nothing that was a major surprise to the team. Because the property is a Grade II listed building, it means for some items, such as replacement of the old wooden windows which are rotten, planning permission from the local borough council is required. Currently, IIMS is in discussion with the conservation planning officer at Fareham Council to seek the necessary permissions.
The scope of proposed renovation works and repairs to be undertaken at Murrills House is, in brief, as follows:
– Re-bed all hips and ridges on the east sides slated roof and inspect all valleys for damage.
– Any slipped and broken slates will be made good, replace all cracked and slipped clay tiles on the rear extension and repoint the ridge.
– Re connect the rear down pipe to run down the roof and into the guttering.
– Repair the cracks in the render on the front rounded elevation of the property.
– Supply and fit an ACCO drainage system to the east elevation along the tarmac footpath to take any surface water away from the building.
– Repair cracked soffit where soffit brackets are fixed, supply and fit 3 new vents to the extension soffits.
– Supply and fit a 200mm layer of quilted loft insulation to the 100mm of existing insulation. Spray all timbers in the loft with a wood boring insect treatment and rot treatment, supply and fit 4x vented roof tiles.
– Box Sash windows to be manufactured in joinery grade softwood timber with Sapele hardwood sill sections. All windows to match identical appearance and design as originals 4mm clear toughened glass face puttied into frames.
West side elevation
To supply and fit 7 no. box sash windows: 1600h x 1000w
South entrance elevation
To supply and fit 2 box sash windows to the first floor: 1600h x 1200w
To supply and fit 2 box sash windows to the ground floor: 2100h x 2100w
East side elevation
To supply and fit 1box sash window to the ground floor: 1400h x 900w
To supply and fit 1 bay window to the ground floor bay window: 2400h x 2400w x 600d
– Main entrance doors. Reuse original existing doors, but supply and fit new frame and make good internal damage around door.