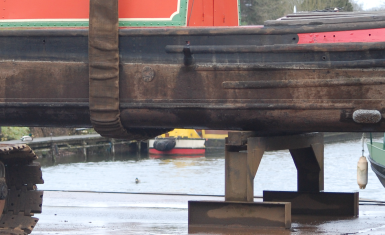
Feature article written by Alan Broomfield MIIMS, who tackles the thorny subject of overplating on steel hulled vessels, in particular Dutch barges and Narrowboats.
It is common practice when in the field surveying steel vessels to find mild steel plates welded to the hull, a practice regularly carried out on leisure vessels as a permanent repair. If any defects are found on the shell of a metal boat during a survey, surveyors are all too quick to recommend that the area concerned be overplated. Marine surveyors who deal with steel vessels will find that very often – Dutch barges and canal boats in particular – are frequently heavily overplated and should remember at all times that such overplating does NOT constitute a repair. It merely hides the defect.
I have recently seen an overplating welded job done to an existing doubling plate on a Dutch barge moored on a gravel tidal mooring. The result was a two foot crack in the second over plate allowing water to down flood between the plates nearly sinking the vessel which was only saved by the occupants having sufficient bilge pumps to keep her afloat until she could get into dock.
I feel overplating should never be allowed on an existing doubling plate even though such bad practice is often found. It is a very bad practice and should be condemned and highlighted within our reports. If doubling or overplating is found on a vessel, the marine surveyor should remember the Law of Unintended Consequences.
Wherever possible, doubling or overplating should be avoided and any defective steel cropped out and renewed. It should never be carried out on round bilges and never doubling over existing doubling plates. However, one occasionally sees this and it should be strictly taboo.
Doubling or overplating can only ever be regarded as bad practice, a cheap bodge job and is intellectually dishonest. It is often carried out on leisure vessels to cover over areas of pitting which is not necessarily the best solution. Pitting, if small in area and localised, is often best dealt with by back filling the pits with welding rather than extensive overplating. Pitting on non structual interior bulkheads can often be satisfactorily filled with a plastic metal paste such as Belzona but this method of repair should not be used on shell plating. Plastic metal should only be used on single pits on water/ballast tank plating or in areas where heat is not allowed or unsafe (fuel tanks).
Finally, the marine surveyor should remember that overplating, though a common practice, is often carried out without thought as to the unintended consequences.
We should realise that it adds weight to the vessel’s structure without adding much compensating volume and, as a direct result, the vessel necessarily sinks lower in the water. It also has a number of other unintended and often unrealised side effects.
1. By increasing the draft, it reduces the available freeboard and, therefore, the amount of reserve buoyancy.
2. It also, therefore, reduces the transverse metacentric radius (BMT), and slightly, increases the height of the centre of buoyancy (KB) usually with very little compensating reduction in the height of the centre of gravity (KG) so that the end result is a reduction in the metacentric height (GM) and a negative alteration to the characteristics of the statical stability curve i.e. a reduction in the maximum GZ value and the range of positive statical stability. [The average metacentric height of a narrowboat is about 150 mm (6 inches)].
3. It may also, depending upon where the overplating is sited, alter both the longitudinal trim and the transverse heel of the vessel with further indeterminate alterations in her statical stability curve.
4. It lowers the deck edge immersion angle and, therefore, any downflooding angle(s).
5. The double plating is usually not secured to the primary supporting structure – the shell side framing. It is also rarely fitted with centre plate plug welds and is dependent only on the edge weld for security.
6. The double plating is secured only at its edges and the greater the area of plate, the smaller the length of the attachment weld per unit area and, therefore, the greater the stresses in those welds.
7. The corrosion or pitting, being the reason for fitting the doubling plates, means the corrosion or pitting will still remain there and, if it is on the inside of the original shell plate, will still be increasing. Doubling, therefore, is merely hiding the problem, not repairing it.
The marine surveyor should remember that time spent considering the consequences of his actions is never wasted. A lot (too many) of boats, particularly inland narrow boats and private pleasure boats, are doubled or over plated to various degrees in both terms of area and quality of welding and finish. When presented with a vessel that has a length of 6 mm plate some 250 mm or so wide welded astride the normally laden waterline, it is not unreasonable to conclude that the plating in way has severe corrosion or pitting (for whatever reason) and that somebody in the past has recommended overplating as a cure.
At this point the marine surveyor’s mind should go into cause and effect mode and ask “How extensive was the defect? Could it have been more simply rectified by grinding out and back welding an area of pitting? Was the corrosion arrested before the doubling was fitted?” That said many of those questions are academic as the answers to most of them are well and truly hidden from view which only leads to speculation. In cases where the marine surveyor finds the situation described applied to both sides of the hull, another question arises – “Did both sides of the vessel’s hull exhibit the same degree of damage or was the double plating simply applied to both port and starboard sides to ensure maintenance of lateral stability or appearance?”
If the plate is badly pitted or where the actual thicknesses, as measured, of bottom or side shell plating fall below allowable minimum, the metal structure in way requires remedial treatment within time limits to be laid down by the marine surveyor. It is, in the author’s opinion, (and for that matter also apparently that of the MCA who will not allow doubling plates of any size – particularly on passenger boats – to be fitted except as a ‘get you home’ emergency measure) far better to crop out such thin areas back to metal of an acceptable thickness and renew the plate in way although it is accepted that that is more difficult, time consuming and costly.
The marine surveyor should also be aware that the heat from the welding and subsequent cooling in air alters the microstructure of the steel and, if a doubling plate is fitted, the underlying steel becomes brittle and can fracture, particularly in cold weather.
Care should also be taken when doubling plates pass over a riveted seam or butt as the weld can draw the nearby rivets causing them to leak. It is good practice where a doubling plate edge traverses a seam or butt to cap weld the rivets alongside the cross over point. Even that has to be done with care otherwise an inordinate amount of time can be spent rivet chasing. It is a common experience, particularly in Dutch barges and canal boats, to find the whole of the bottom doubled. That clearly begs the question as to the condition of the original shell plating underneath the doubling plates and the marine surveyor should be very wary indeed of vessels that have had so much overplating.
The US Coast Guard states that, in certain cases which they do not define, a welded doubling plate may be used in lieu of a crop and insert repair for the permanent repair of small damaged areas lying wholly within an individual plating panel but they also, quite rightly in the author’s view, do not allow the use of doubling plates in the strength deck, bottom or shell plating or part of the main hull strength girder. They also state that such doubling plates or patch plates in American terminology – are inadvisable in areas of high corrosion and the author would most certainly concur with that.
Doubling plates also tend to rust from the inside faying surface outward.
The marine surveyor should note that, when an area of plating is doubled, the presence of these doublers creates a structural discontinuity. That may induce rather than prevent a structural failure. We should also note that doubling plates tend to proliferate as randomly placed items that, in reality, tend to cover up deficiencies that would otherwise show up the true condition of the hull. It is also common practice to leave such doubling plates with square corners.
This is bad practice as it raises a hard spot on the corner from which cracks in the shell plating may propagate.
When the marine surveyor comes across existing doubling plates with square corners he should closely inspect the shell for cracks using a dye penetrant if thought necessary. Doubling plates can also flex and vibrate causing the edge welding to crack. If such cracking is found here, again, a dye penetrant is useful to find the extent of the crack.
The marine surveyor should also be aware the estimated plate frequency be checked against the revolutions per minute of the main engine (and the generator engine if fitted) and also against the propeller blade frequency. i.e., the shaft revolutions multiplied by the number of propeller blades. If the ratio of any of these factors to the estimated plate frequency is a whole number then it would be as well to investigate the possibility of engine or propeller excited vibration causing the cracking. The marine surveyor should bear in mind that steelwork repairs and plate replacements are never cheap but that the potential consequences of not carrying out proper repairs are far more costly and traumatic.
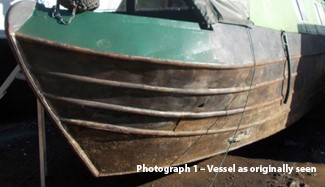
These factors made me put pen to paper when I was recently asked to look at a narrow boat which had been purchased without a survey that being the first mistake. The owner had the vessel out of the water for blacking and had decided to have the hull thickness determination for future maintenance.
The vessel had a doubling plate close welded between the whisker harpins on the port bow. I was suspicious of the area around and behind the doubling plate due to the poor quality of the welding and suspected the latter to be porous to water ingress as the plate was below the water line.
The upper whisker harpins were found to be suffering from jacking corrosion which had been instigated from the D bar only being stitch welded along the top and bottom of the bar which is also a common defect found on such vessels as the builder can save time and money by not seam welding such bars.
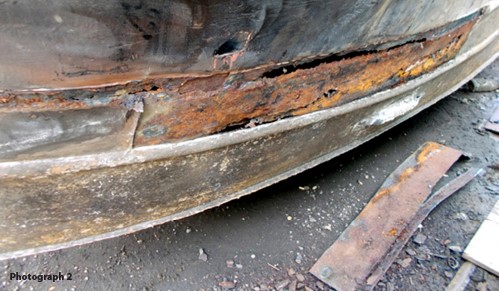
However, the defect in this case was compounded when the shell plate was found to be holed above the harpin. The hole can clearly be seen in Photograph 1 which shows the area of the vessel as first seen. It was also noted that a poor repair had been carried out below the lower harpin forward and the shell plate was also found to have excessive pitting just aft of the stem.
The upper harpin and doubling plate were cut off while I was on site by grinding off the welds and Photographs 2 and 3 show clearly the heavily corroded inner repair plate and appalling condition of the underlying shell plate.
Photograph 4 shows the faying surface of the doubling plate that was removed and which can be clearly seen to be corroding from the inside outward. It can also be seen in this photograph the doubling plate had been welded to the harpin in places making the doubling plates seam weld porous to water to entering between the doubling plate via the gaps created when the D sections harpins were originally stitch welded in manufacture. The fault would have been compounded by crevice corrosion and a poor maintenance programme though out the vessel’s life.
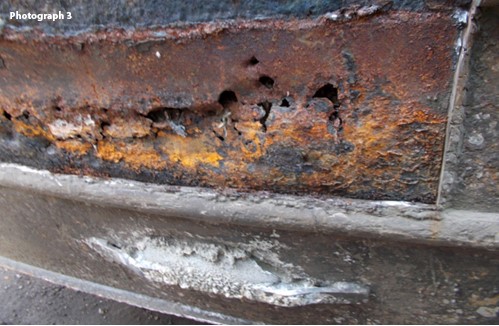
The only possible repair to that damage is a complete crop out of derogated steel work and new steel close welded in to the aperture and new D section bar fitted to the shell side and which should be seam welded fully along the top and bottom of the bar.
In a recent video available on the web, a broker was seen to be stating that the narrow boat he was showing required the whole side to be doubled because of a single pit (apparently due to microbiological attack) that had been found by a surveyor. He also stated that the doubling would increase the strength of the hull and give the vessel an extra life of twenty years. Both statements are clearly nonsense.
However, overplating is a repair that is regularly accepted by brokers and the pleasure vessel users community and it is our duty to educate them that these repairs are not a cheap way out.
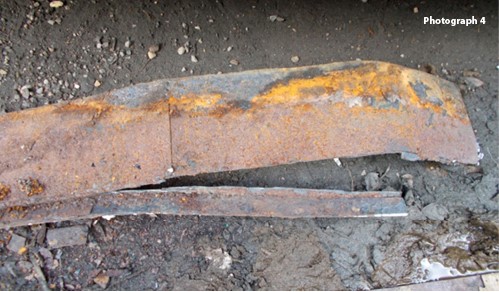
Patrick Keating, who regularly lifts narrow boats at South Dock, has stated that he has seen a number of such vessels where the bottom plating was sagging because the whole area had been doubled and where the doubling plates were unattached to the frames or even the remains of the original bottom plate.
He stated that, on one vessel, the welder, who was about to work on it, started to cut out a section of plate and, as soon as the plate was broached, water started pouring out. The bilges were immediately checked and found to be dry and it was estimated that at least 500 litres of water had been trapped between the doubled bottom and the original shell with the water getting between them from the bilge through holes in the original bottom plate.
I have also seen water pouring out from doubling plates on the shell plate sides through pin holes found in the seam weld whilst carrying out survey’s and try to make a point of viewing the vessel being lifted from the water.
The obvious problem with this practice was that the doubled shell plating can corrode from the inside out with no external evidence of the problem is not usually seen and can often go undetected until too late. In recommending the fitting of doubling plates the marine surveyor must take even more into account than the increase in draught and loss of freeboard due to the added weight. For example, a forty foot long narrow boat will have a tons per inch immersion value of about 0.55. If her bottom is fitted with a 6 mm thick doubling plate over about 30 feet of her bottom by the full width she will sink by about 1½ inches with an equal loss of freeboard plus a deleterious change in her metacentric stability and down flooding angles.
Here it is probably apposite to quote the case of the narrow boat MINI MOO ex MARY MINT. The following is quoted verbatim from a Safety Bulletin issued by the Port of London Authority: –
On the 24th August 2012, a narrow boat was delivered by road to South Dock Marina in London for a new owner. The vessel was lifted into the dock and the new owner requested to lock out of the marina as they had an overnight berth in Lime House Marina; a short distance up the River Thames. The vessel departed the lock at 17:00 with 5 adults and 1 dog aboard. As they departed the lock the lock keeper commented to them that they should have lifejackets on board as they appeared to be missing. The crew decided to continue on and left the lock with 3 adults in the aft cockpit and 2 adults in the cabin. The vessel transited directly across the river to the starboard side of the channel and then turned upriver towards Lime House Marina. Shortly into their transit the crew noted a change in the engine note and opened the engine room hatch to find the engine half submerged. All persons quickly moved to the stern to try and bail out the engine room, but were unable to cope with the ingress of water into the vessel. The engine room continued to fill with water and flooded into the main cabin, submerging the aft coaming below the water, resulting in severe flooding of the vessel which sank within 10 seconds. All of the crew and the dog entered the water without lifejackets, but were rescued by a nearby RIB and Police Launch.
Marine surveyors and others concerned with narrowboats should obtain a copy of the Bulletin from the PLA and take note of its recommendations.
It was noted by the PLA that the vessel had been the subject of extensive overplating. Whoever had recommended the overplating had also recommended partly blocking off the engine room air jalousie on the port side as its bottom edge was considered even then to be too near the waterline. The following Figure 1 below shows the effect of the overplating and the number of persons seated aft.
The buyer of the MINI MOO bought the boat on the strength of a survey report provided by the seller. The marine surveyor concerned had estimated the height of the engine air intake jalousie from water level marks on the hull although the vessel had been out of the water for a considerable time prior to his survey. He had estimated the intake to be 200 mm above the waterline but when it measured after the salvage it was only 65 mm. The marine surveyor had covered himself with the caveat that it was an estimate only. In that particular case, when the vessel sank, no life jackets were on board and at least one person on board could not swim. The survivors were very lucky that nearby boats managed to pluck them from the water immediately. The fact that a marine surveyor’s report perhaps covers him with words such as estimated does not provide much comfort if bodies have to be pulled from the water.
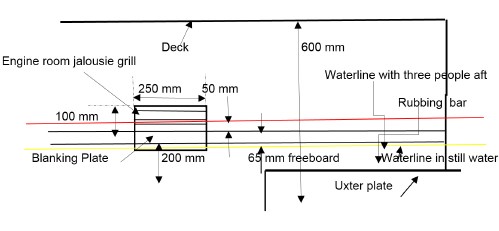
Figure 1 Detail of Engine Jalousie on MINI MOO
The yellow line indicates the original free board in still water this was meassured to be 65 mm. The red line indicates the waterline incurred from three people standing on the aft deck which pushed the engines jalouise below the water.
The vessel was fitted with an air cooled Lister engine and, in accordance with common practice, had a ventilation jalousies cut into the topside aft to give the necessary combustion air supply for the engine. The overplating was such that the jalousie at the engine room was within 65 millimetres of the waterline. That highly dangerous situation was not helped by the presence of a small lop on the water surface. Some five people plus a dog called Gus were on board (three of them sitting aft and two in the cabin) to make the journey and, hearing unusual noises from the engine, the engine room cover was lifted and the boat was found to be rapidly taking water. The situation was made worse by all of the people on board moving aft to have a look and to try to bale the water out, thereby increasing the trim and pushing the lower edge of the jalousie 50 mm under the water. The boat rapidly filled and sank within 10 seconds but, fortunately, a nearby RIB and a police boat arrived within two minutes and all personnel, plus Gus the dog, were picked up by the police and the nearby RIB. Despite the fact that none of them were wearing life jackets and at least one of them could not swim, there were, thankfully, no fatalities although all were suffering from shock. What Gus said was not recorded. It was later said that the owner had relied on a marine survey report prepared for the previous owner and that the vessel was uninsured.
Following the discussed casualty, the author recommends that the following paragraph be included in any relevant survey reports.
The Port of London Authority has recommended that the tidal reaches of the river Thames which stretches from Teddington Lock to the Number One Sea buoy be regarded as MCA Category C waters as wave heights of up to 1.2 m may be encountered there. We would recommend that the similar tidal reaches of the river Medway also be so classified. Narrowboats with engine room side jalousies are simply not suitable for operation on those waters.
Another point is that not all Narrowboats have a very small transverse metacentric height often only a matter of 150 mm or so and heel very easily and the minimum angle of down flooding through the jalousie in the case discussed was not more than about 4 degrees which is far too small for safety even on the calm waters of a British canal. Further, the average first down flooding angle of a narrowboat even without such engine jalousies is often less than 35°. The minimum recommended angle is 40°.
Whilst in the same yard I had carried out a survey on a Springer steel cruiser style narrow boat which had been constructed originally from 3 mm mild steel plate due to its age of the vessel was probably constructed of 1/8 inch Imperial steel plate. This was found to have been over plated with mild steel plate of 5 mm thickness along and below the waterline. It is a misconception by boat yards and brokers that all vessels that fall below 4 mm plate thickness should be fitted with a doubling plate along those areas.
However the fact of the matter is, a repair is only required if the parent thickness falls below 20% of the area within a single plate, at this point that section should be cropped and replaced with the same sized thickness of plate for example if the vessel is made of 3mm mild steel plate a suitable repair would be to fit a new close welded 3 mm mild steel plate which should be welded in to bring the vessel back to the original scantlings. The mild steel fitted should also be of ship building quality.
One final but very important point to remember is that many Dutch barges and similar steel vessel when converted to floating homes have the inside of the shell coated in sprayed plastic foam or a mixture of horse hair, goose fat and tar. Many of such foams and coatings are highly flammable and if set on fire can give off large volumes of highly toxic gases. Welding a doubling plate onto the side of such a vessel, therefore, poses a very high fire risk with possible resulting fatalities. BEWARE!
One way to overcome the fire risk is to close and seal all doors, windows, scuttles, ventilator and other opening and then to fill the sealed off space with carbon dioxide. The gas will kill any fire before it starts. It is, of course, necessary to make sure that, when the welding work is finished, the space is fully opened up and thoroughly fan ventilated to ensure that there is no CO2 left inside the hull. Do NOT enter the hull until that has been carried out.