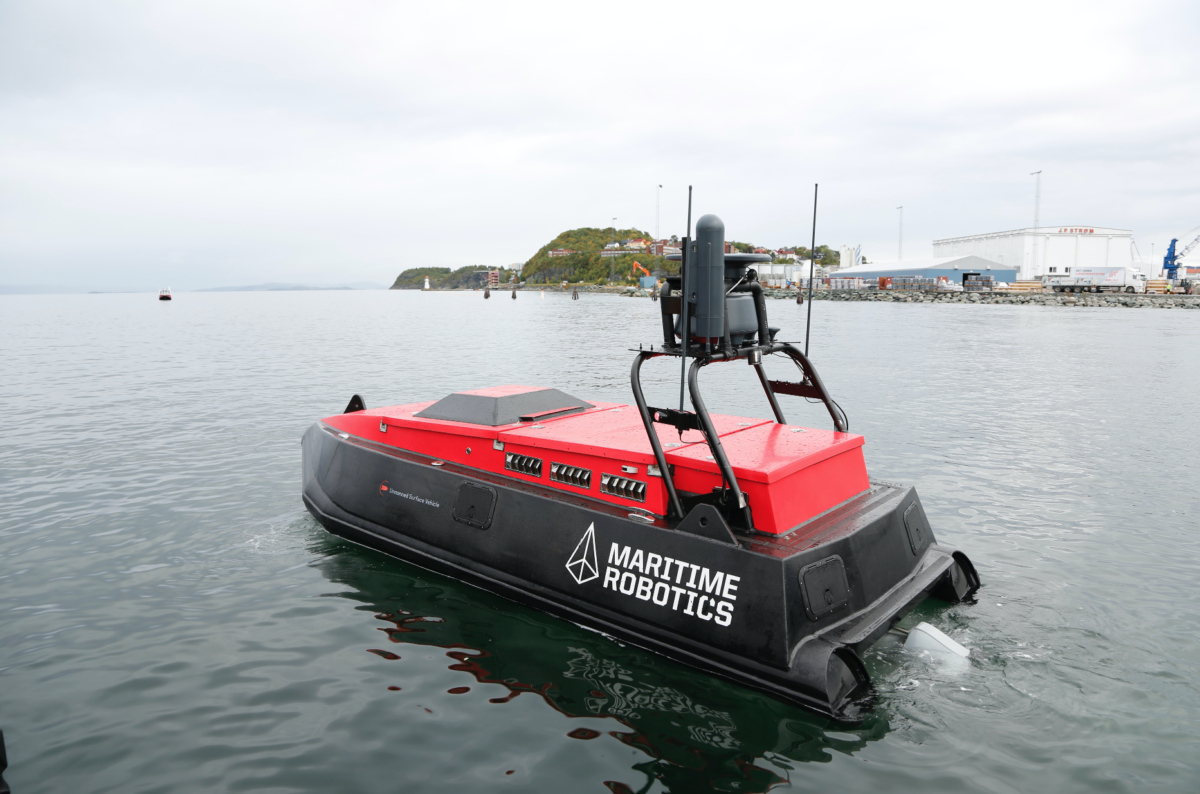
Automation presents a set of unique challenges to designers, insurers and operators of ships. In this article, reprinted from the Shipowners P&I Club website Keir Gravil, a naval architect at Frazer-Nash Consultancy in Bristol, UK discusses some of the key issues that could face automated ships of the future from a design perspective.
It is a truth recognised by many industries that the future of transportation lies with greater automation. Over the last 50 years we have seen huge changes not only in shipping, but in every form of transportation and vehicle. Aircraft now incorporate automation routinely on flights around the world, cars are being developed to drive themselves and many railways have been totally automated for some time. As each step in the evolution of transportation progresses, the human element of control is reduced or eliminated altogether. But what of shipping? Surely an industry the size and scope of international shipping faces unique challenges in the realm of automation?
The background
It is often the job of ship designers, especially those in the naval defence industry, to think ahead and anticipate future technological changes. One could argue that a particular quirk of defence, with its long lead times for new platforms, is that ideas more at home in science fiction are actively considered for future ships. Commercial drivers are usually shorter term: a commercial ship owner can’t wait decades for delivery of a new vessel. The naval industry appears to have taken a lead when it comes to automation aboard ships, with tight budgets, crewing concerns and ever more complex weapons and propulsion systems meaning automation is an attractive solution to the problems faced. Indeed, HMS Queen Elizabeth, the Royal Navy’s new aircraft carrier’s weapons handling system can be operated by a team of 50, or as low as 12; said to be a reduction of over 65% compared to more traditional systems1.
Crewing challenges are by no means unique to naval ships: commercial ship operators face similar problems, with a predicted shortfall of around 150,000 officers in the maritime industry by 2025. Increased automation is an obvious and attractive solution to the challenges faced by ship owners, operators and the wider industry. But how far is this likely to go and what hurdles will be faced by those tasked with delivering this automation?
Ship design considerations
Ship design is by no means a straightforward activity. Depending upon the role of the vessel, the design requirements, stakeholders and regulations underpinning its construction can be vast and complex. Adding automation into the mix presents its own set of design challenges and opportunities, and will require significant cooperation between ship owners, ship builders, classification societies, underwriters and P&I Clubs. Automation will not happen overnight; it will be a gradual change, but many are predicting ‘crewless’ ships sailing the oceans in the future. The challenge this poses for ship design is both exciting and formidable.
The obvious benefit to increasing automation is the reduction in operational crew numbers, or even the abolition of crew altogether. Ignoring the obvious regulatory hurdles, this reduces the need for accommodation and crew welfare systems. But to describe crews as merely ship operators is doing them a disservice: they keep the ship running smoothly and without incident; they react to unforeseen circumstances and solve complex problems with navigation and machinery performance. This is no mean feat to achieve with automation.
Reduced crewing offers opportunities however, ships could potentially be made to be more efficient. Superstructures designed to accommodate crew and provide sufficient navigational field of view could be removed, or changed to reduce wind resistance. Internal layouts could be optimised, with more compact systems. All these could provide benefits in terms of a reduction in operating costs, especially that of fuel.
From a survivability perspective, standards underpinning the integrity of a damaged ship may need to be revisited. With no crew available to respond to fire or flood, the criteria which the ship should meet could become more onerous, with increases in the number of flooded compartments a ship is expected to survive, and resistance to fires in machinery spaces.
Ship systems
Humans are capable of the complex decision making and logic required to keep machinery in peak order and to keep the entire ship safe and navigable. Replacing this with technology would be difficult, but not impossible. There would be a need for greater redundancy to account for machinery failures; with no crew a failed piece of equipment could not be fixed instantly. Whilst systems supporting crew welfare might shrink or be removed altogether, other systems could grow in size due to this increased need for redundancy. Ship operators might also start to demand higher levels of reliability from their equipment suppliers, to ensure continued vessel operation.
Propulsion architecture could also change to reduce the risk of total failure. Slow-speed diesel engines might make way for fully electric multi-engine architectures, ensuring continuity in case of failure. Whole systems could be duplicated to allow for a simple switch-over, negating problems until the ship arrives in port for repairs. Modularity may become a key requirement, enabling a ‘plug-and-play’ approach, so faulty equipment can be removed and quickly replaced in port.
In addition to the duplication of familiar systems, new systems would be introduced or expand. Communications to shore-based installations and satellites would be a greater priority, and the bandwidth required for achieving automation would grow. At some point, a ship owner will need to check what is happening on their automated platform; the operating performance, location and condition of the ship will need remote monitoring, and commands will need to be delivered and acknowledged. The computational equipment needed on board would expand significantly to meet the complex demands of automation and remote communication.
With many ship control systems experiencing significant growth, initial capital costs for procurement would increase. It is likely that ship owners and operators would place more emphasis on minimising through-life costs, to offset the increase in the capital costs of purchase. The testing and commissioning of systems (especially automated safety-critical systems) could add a considerable burden to the commissioning and trials phases of ship design and construction. Ultimately, the need for more complex systems from the outset could push the cost burden to earlier in the ship’s life cycle, and this would need to be balanced by lower operating costs.
Operation and control
Perhaps the biggest technical hurdle is the command and control of ships globally. Some industry players are already envisaging ships operated remotely from land-based control rooms, but remote operation has significant challenges, both technical and financial. Technically it is certainly feasible, with Rolls-Royce and Switzer recently teaming up to operate a tug boat remotely in Copenhagen harbour. However, this technology is far from mature and is yet to be seen operating successfully in the open seaways.
A major challenge for designers and operators is that of data. Handling and communicating large amounts of data will be of huge importance in the age of the fully automated ship. Reliable and secure channels of communication will become increasingly important for remote operation and will require a constant data connection. This will come at a cost – currently satellite data is around $US4.00 per megabyte – although this may decrease in the longer term. Not only will the transmission of data be important, but the security of ship systems to breaches in cybersecurity will become a greater priority. Designers will have to ensure the resilience of ship systems and enable swift reactions to potential breaches. Whilst piracy today sees physical attempts to board ships (and this might not necessarily change with fully automated vessels), piracy of the future could involve nothing more than a laptop and remote connection.
The safety of autonomous control systems is also an area requiring significant consideration. Testing automated safety-critical systems, for example, will need to be significantly more demanding than at present. From a platform perspective, designing autonomous ships with the processing power to safely navigate around the world will be a major challenge. Safety is critical to any operation, and essential systems will have to achieve very rigorous testing, commissioning and operation standards. The accidents seen in the testing of driverless car technologies would be totally unacceptable with a large ship.
The final hurdle, and likely the most onerous, is that of trust. Ultimately, the implementation of automation in any vehicle requires the trust of the human beings aboard, or of those who have responsibility for the vessel’s actions. Humans have been mariners for millennia, from those first crossing the seas on small wooden sailing boats, to those working aboard the largest vessels today. Whilst technology will inevitably rise to the challenge of automation, getting a ship to sail without a master and crew will likely prove to be the industry’s greatest challenge.
There are already plenty of organisations, like Frazer-Nash, thinking about the future of automation in shipping. With the development of physical demonstrators the future is already here. Frazer-Nash has worked on autonomy across many industries, including shipping, and envisages a significant amount of further development in the years to come. Automated ships are closer than we think, but the design challenges and regulatory issues surrounding them are still far from solved.
Reprinted by kinf permission from Shipowners P&I Club https://www.shipownersclub.com/