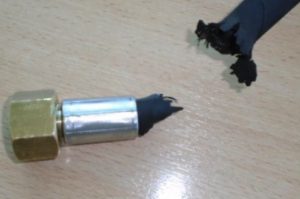
In its latest Safety Flashes, IMCA presents a case of a fire due to incorrectly selected oxygen welding gas hose, during a routine cutting job onboard a ship. There were no injuries or ship damage, but investigation later revealed that the hose had been recently replaced with one that did not comply with ISO 14113 specification.
The incident
The ship’s welder opened the Oxygen and Acetylene gas bottle valves in order to do a cutting job on deck. These gas bottles were attached to the vessel’s integrated welding gas system. Opening the valve on the Oxygen bottle caused an explosion to a short, high pressure hose delivering oxygen from the bottle to the oxygen gas regulator. The end of the hose caught fire and was quickly extinguished by turning off the oxygen bottle. Nobody was injured and the only damage was to the hose that completely separated.
Findings
The hose had been recently replaced, but the replacement hose was a hydraulic oil service hose with oxygen fittings. The replacement hose was not compliant with the ISO 14113 specification required by the manufacturer, although the pressure rating was suitable;
The non-compliant hose was supplied from a non-preferred supplier (the required hose length was not available from original supplier);
The onboard team did not adequately check that the hose was of the correct specification.
Lessons Learned
Welding hoses should be compliant with ISO 14113. For oxygen hoses, the material should have an auto-ignition temperature suitable for the service (typically > 400°), and cleaned for oxygen service.
Do not assume that because a hose is sufficiently pressure rated it is fit for a specific purpose.
Always ensure correct specification hoses are ordered and received.
IMCA notes that in order to avoid adiabatic compression:
– Use only original equipment and spares when handling/servicing oxygen equipment;
– Work clean – no oil or any other hydrocarbon impurities must contaminate the parts (your hands, tools etc.);
– Open oxygen cylinder top valves slowly.