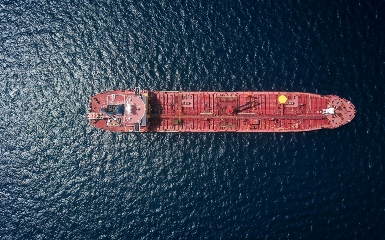
According to the American P&I Club, the ingress of seawater through leaking hatch covers remains one of the most significant causes of cargo damage aboard dry cargo vessels. Cargo damaged by water leaking through hatch covers can result in large claims and affect Members’ claims records. Most leakage problems occur because of poor maintenance. Hatch covers will leak if:
– compression surfaces are not aligned correctly due to worn bearing pads, locator and/or stoppers;
– gasket sections are damaged, missing, worn, over compressed or inserted in short lengths;
– there are cracks or holes in the plating; or
– there is permanent overall distortion of the hatch covers.
Members have an obligation to exercise due diligence in ensuring that hatch cover maintenance and regular weathertightness testing is conducted on board their vessels as an integral part of each vessel’s planned maintenance system. This should include the following steps:
– The creation of a detailed shipboard maintenance plan based on the hatch cover manufacturer’s build, operation and maintenance specifications.
– The provision and upkeep of adequate spare parts and seals.
– Crew training to ensure the proper implementation of the shipboard maintenance plan.
– Shore based management’s commitment for close follow-up of the maintenance plan and its implementation.
– Regular testing, and logging results, of hatch weathertightness by the vessel’s crew and/or independent surveyors using high-pressure hose testing, or preferably by testing with approved ultrasonic hatch leak detection instruments. In reference to step 5 above, although high-pressure hose testing before loading cargo in combination with chalk imprint testing are helpful indicators of hatch covers’ weathertightness, the exact location of any leaks that may occur are almost impossible to pinpoint and repair due to the tendency of water to travel laterally from the point of ingress. This is the case, even though these methods are accepted by some classification societies as a Load Line Certificate verification item, because any minor leaks of water should not affect stability of the vessel.
In addition, a hose test can show whether the physical contact between rubber packings and their mating surfaces are satisfactory in static conditions. With the hose test, however, the compression of the rubber packings cannot be assessed. When the vessel is at sea, and in dynamic conditions, even in a in case of light movement, only a small distortion of the hatch covers could result in the hatch cover panels flexing, and under these circumstances the water may find its way to the hold.
On the other hand, an over-compressed rubber packing may also lose its sealing capability while in dynamic conditions at sea, since its rigidity will
not be able to compensate for the vessel’s movement. Accordingly, a chalk test or hose-test cannot guarantee the weathertight condition of the hatch covers and may affect various cargoes that are sensitive to water contamination, wetness or even moisture content in the air.
Ultrasonic equipment uses sounds with frequency above 20 KHz that cannot be heard by the human ear. It can more reliably indicate the integrity of the packing rubber and its ability to compensate for movement between the panels and the hatch coaming (as well as in between adjacent panels) when the vessel is at sea, and in dynamic conditions. This is crucial in preventing water ingress.
The ultrasonic emitter is placed in the center of the cargo hold tank top with hatch covers open, activated and the operator of ultrasonic testing (UST) equipment then measures the open hatch value (OHV). Then vessel’s crew close hatch covers, and the operator of the UST equipment checks for ultrasound signals passing through the rubber packing and compression bar interface of the hatch covers and records the location of any leaks for subsequent repair or adjustment of the packing. The acceptable range of leakage is less than 10% of the OHV. Any discontinuity in the seal (e.g., missing or damaged rubber packing) or area with lack of compression (e.g., wavy or deformed compression bar) will allow ultrasound to pass and the leaky spot identified as an area of concern.
The ultrasound tightness testing of the hatch covers is an accurate, non-destructive method, which can be used under all weather conditions without the risk of damaging the cargo during testing, allowing easy detection of the defected areas/points, thus facilitating appropriate
repairs, if required.
The Club recommends that Members equip their dry cargo vessels with ultrasonic hatch cover leak-detection instruments to be used by the vessel’s crew to regularly check for weathertightness. The cost of such prudent investment will amount to far less than any potential cargo claim that could have been avoided by detection and repair of leakage areas prior to potential water damage.
In addition, Members stand to avoid imposition of general defect and water ingress exclusions on cover should a vessel fail weathertightness tests during its initial P&I condition survey, and the additional cost and inconvenience of a follow-up survey for re-testing.