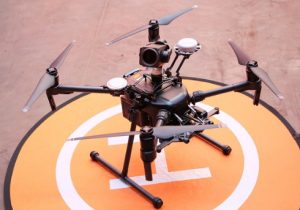
As part of an on-going focus on safety in enclosed spaces, ClassNK describes how it has carried out detailed drone tests to revolutionize ship surveying. In spring this year, ClassNK introduced guidelines on the use of drones in class surveys, covering procedures and technical considerations for safe operation, as well as requirements for drone service suppliers.
Although drones with multiple propellers on the same plane are currently the most widespread design, research is taking place into alternative arrangements with tilt rotors and propellers in a tetrahedral configuration. Meanwhile, significant progress has been seen in autonomous operations using higher precision positioning, and considerable advances in machine image recognition and processing.
Typically equipped with a compact camera for photography or recording video and Wi-Fi for data transmission, these easy-to-control, lightweight machines have rapidly grown in popularity. Apart from the consumer hobbyist market, and use for product delivery by online retailers, drones have attracted interest from across industry: they are ideal for collecting images from high or otherwise inaccessible or dangerous locations. They can be utilized for a range of aerial photography, inspections and surveying, and security applications, and have proved invaluable in planning rescues and emergency response.
In the maritime industry, efforts are underway to use drones for inspections and surveys. In fact, discussions on Remote Inspection Techniques (RIT) are already well-advanced at the International Association of Classification Societies (IACS), which published revised guidelines on remote inspection techniques in June 2016. The revisions of the associated IACS Unified Requirements are complete and will take effect in January 2019.
Deploying drones on ships presents some significant challenges. The drone may not function properly in the cargo hold or ballast tank due to being in an enclosed space surrounded by magnetic material which may interfere with some of its sensors – particularly GPS and magnetic compass – that are tightly linked to flight stability. Dark environments can also make it difficult for operators to fly drones safely.
Last September, ClassNK designated ‘survey technology innovation’ as one of four focus areas listed in its new R&D Roadmap, with drones identified as a key technology. The society has been verifying drone performance, with test flights conducted in a variety of enclosed spaces of the sort found on ships.
Assessing basic performance
A basic performance verification test was devised to demonstrate maneuvering (take-off and landing, forward/reverse and lateral flight, reverse flight with 180-degree yaw) and to assess the capabilities of camera and sensors. The camera performance was tested with a Landolt ring chart – the kind of chart opticians use to test eyes – to evaluate definition of different line thicknesses from 0.1mm to 5mm, and a QR code. Differences in results were observed when the subject drone, a Phantom 3 Standard from DJI, was operating with and without GPS signal. Maneuverability tests in the vicinity of a powered-off crane to assess antimagnetic performance were also carried out.
The outdoor maneuvering test took place in windy conditions, which significantly influenced the results. While fixed-point hovering was easier when using GPS, the gain was large causing the drone to over-compensate in its movements. In non-GPS mode, the gain was small and smooth maneuvering was possible, but wind-thrust had a more marked effect on the drone.
In GPS mode, the drone immediately begins hovering when the operator removes his finger from the controller, whereas in non-GPS mode, inertial force continues to move it until a counter input is given. Consequently, non-GPS mode gives a manual feel to maneuvering and it is possible that operators will find the drone easier to control. When the wind subsided in the trial, stable flight was possible regardless of GPS availability.
Indoors with no wind, stable flight was possible both with and without GPS. Since these results were obtained with a low-cost drone, it is conceivable that higher-end drones equipped with ultrasonic sensors and other advanced features will be even more stable.
Many images photographed with the camera were extremely clear. However, because this model lacked an optical zoom, enlarged images were often indistinct. Image sharpness distinctly improved when the drone was flown closer in to its target. In survey applications, optical zoom would be an essential requirement. Camera specification and artificial lighting will also need to be considered if photography in dark environments is deemed necessary.
The tests in the material storage yard with a crane threw up some interesting results. The drone initially failed to take-off, with the system displaying a ‘compass abnormality’ error message. However, when launched from a more magnetically benign location, the drone was able to approach the crane without the issue. This suggests performance in the presence of magnetic structures must be carefully evaluated before a drone is deployed to carry out inspection work.
Tests in simulated tanks
To simulate conditions inside a ship’s tank, a drone was put through its paces in a land-based, steel test tower. The experiments, using a DJI Matrice100 drone, studied the impact on performance due to compass unreliability, intermittent or complete lack of GPS and poor lighting both for flight control and photography.
Take-off was possible when the drone was placed more than 50cm away from magnetic materials, i.e. the steel walls. There was no difference in attaining stable flight between GPS and non-GPS mode, revealing that drones are operable with only basic inputs from gyro and accelerometer. Piloting a drone that has relatively low control precision is a good way for operators to accumulate experience.
When flying near walls, there was a slight shaking in the drone motion, owing to the wind from the drone’s own propellers. To prevent collision with walls, it may be necessary to attach a guard or collision prevention device.
Images taken inside the tower were generally of low quality, due to a combination of poor light conditions, small camera sensor size, and inappropriate ISO settings. Artificial light sources, both from ground level and mounted on the drone itself, resulted in improved images. When the photo subject contains highly polished or metallic surfaces, it will be necessary to experiment with different arrangements in order to produce diffused light that minimizes reflection. Night-vision cameras may also be considered as an option. It was also noted that videos transmitted from the camera were frequently corrupt on the receiving terminal such as a smartphone.
Tests onboard ships
The final phase of the study was directed at testing the performance of drones inside a cargo hold of a bulk carrier and tank of an oil tanker and was carried out with the cooperation of Kanda Shipbuilding and Orient Marine in the first instance and Tsuneishi Shipbuilding and Technos Mihara in the second. Drones used were the 4.5kg DJI Matrice 210 and the 3.5kg DJI Matrice 100.
On the bulk carrier, the trial took place with the hatch half open, providing an intermittent GPS signal and good daylight for photography, so additional lighting was not required. The flight route was based on the path of an actual internal audit. Because the Matrice 210 is an industrial grade drone with sophisticated machine-vision based self-localization, its flight was stable regardless of GPS availability.
Photography was carried out at a distance of 5m, as the drone itself is almost 1m wide. The high-quality camera benefited from both optical and digital zoom. Zoom photography is generally sensitive to vibration or movement, but good results were obtained thanks to the drone’s high stability when hovering at a fixed point.
However, at higher altitudes the downward facing vision system found it harder to capture landmarks on the hold’s uniform ground surface. This inhibited the self-stabilization, especially when GPS was unavailable. In such conditions, manual flight by the operator is preferable.
At one point during the trials both GPS and the vision system did not function at the instant that a compass error occurred. Although the drone drifted, the operator, who had more than 500 hours flight experience responded calmly and kept the flight stable. The exercise demonstrated that safe flight in a hold is possible but highlights the importance of having a skilled operator and choosing a drone with high redundancy for magnetic materials. Furthermore, as the size of Matrice 210 prohibited flight in close proximity to members, there will inevitably be blind spots in surveys with this type of drone.
On the oil tanker, as with the bulk carrier, the flight path was selected according to locations for photography needed in an actual close-up survey. The pilot worked together with an assistant in charge of the camera. A third surveyor checked the images as they came in, requested close-ups when needed, and signaled when to move to the next location. Additional illumination was provided by lights mounted on the drone. This configuration delivered good results for still images but video images suffered from noise.
Fixed-point hovering was difficult because flight was performed in non-GPS mode. The resulting movement caused blurring in photos of members and made pinpoint checks somewhat stressful. This degradation in image quality was exacerbated in zoom photography. During close-up photography, results were heavily dependent on the operational skill of the drone pilot, especially when flying close to walls or other structures. The pilots in these tests had at least 100 flying hours experience.
Compass error occurred and prevented take-off when attempting to fly the Matrice 100 after an extended period of time. Although it is hard to draw definitive conclusions about the effect of magnetic materials, it is thought that the accumulation of error due to the presence of magnetic materials was a factor.
The procedures and best practice given in ClassNK’s guidelines combine the understanding of drone performance gained in these and other trials with its decades of experience conducting class surveys. The society will continue to actively work with innovative technologies like drones and will continue to make efforts to contribute to the further development of the maritime industry.