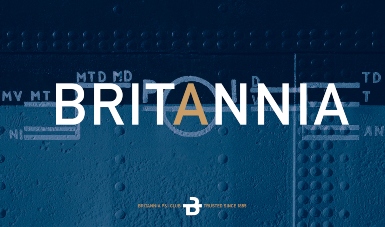
Britannia P&I Club recently became aware of an incident where a number of unfortunate events, including the fall of the vessel’s spare main engine cylinder liner, led to an oil spill on deck.
A ballasted crude oil tanker arrived at its load port early in the morning and contacted the local Vessel Traffic Services (VTS) who instructed the vessel to drift ten nautical miles off the coast to await berthing. The vessel’s main engine was kept on ten minutes’ notice and used to occasionally reposition the ship while drifting. The following night the wind picked up with reported gusts of up to 60 knots and the master decided to use the main engine to counter the heavy rolling.
After about half an hour the main engine was stopped again. Shortly after the engine room advised that a spare main engine cylinder liner had fallen from its securing rack damaging a fuel pump and disabling the main engine. The engine room crew began to move and re-secure the fallen liner in order to restore propulsion. Meanwhile, on the bridge, the second officer noticed heavy fuel oil on the main deck, which he suspected was coming from one of the bunker tank vents. At this point, the vessel was rolling about 30 degrees as well as heaving violently. The master informed the head office who advised the port authorities of the vessel’s condition and a tug was dispatched to the scene to be on standby.
After about 15 hours the engine room crew succeeded in isolating the main engine fuel pump no.1 and restored propulsion. The vessel proceeded to the load port where it became evident that fuel residues had covered a large area of the vessel (over 8600 m2), including the hull, main deck and accommodation block. The terminal required all oil residues to be removed before the cargo operation could commence. The ship shifted to another jetty where a 21-day clean-up operation was conducted.
Probable cause. It is likely that the following factors may have contributed to the incident:
1 Immobilising of the main engine
Once the main engine was immobilised, the vessel encountered heavy rolling/pitching. The rolling resulted in a small oil spill on deck through the vent head of one of the forward bunker tanks. Here the strong wind caused the fuel oil to spread to large areas of the vessel.
2 Securing of the cylinder liner
The liner had been placed and secured during dry dock just a few months before the incident. The arrangement for securing the cylinder liner consisted of two c-clamps: one placed at roughly mid-point and the other almost at floor level. The c-clamps were secured to the steel frame of the cylinder liner rack by a bolt and plain washer through an elliptical hole on each side of the steel frame. From the size of the elliptical hole, it appeared that no washer had been mounted between the nut and the steel frame. Vibrations had then caused one of the nuts securing the top c-clamp to enlarge the elliptical hole until the nut was able to slip through.
3 Heavy weather precautions
According to the chief engineer, the crew members had inspected and secured all loose items in the engine room as part of their heavy weather precautions. However, this did not include a close inspection of the securing arrangements for the cylinder liner.
4 Filling of Bunker Tanks
At the time of the incident, one of the forward bunker tanks was 94.6% filled with fuel oil. An inspection of the bunker tank’s vent did not reveal any structural damage and was found to be functioning as designed. However, although the design of the tank venting system is class approved, the possibility of spillage through the venting system during severe rolling when the bunker tanks are filled to 95% or more cannot be discounted.
Lessons learned
1 Securing: It should be ensured that the appropriate strength is calculated for all parts used to secure the heavy spares and equipment and adequate securing arrangements provided. This should take into account scenarios where the vessel may experience extreme rolling of 25-30 degrees, for example. Only the original securing devices should be used and securing bolts or devices should be protected against loosening due to vibrations.
2 Inspection: All securing arrangements for heavy spares and equipment should be visually inspected both during daily routine inspections as well as being part of the vessel’s heavy weather precautions to ensure they are safely secured. Attention should also be paid to any low harmonic vibrations identified during sea trials, especially in the aft part of the vessel, as these may result over time in fatigue cracks to the engines’ top bracing, which should also be regularly checked.
3 Filling of bunker tanks: The design of certain vessel’s fuel tank venting system may lead to the risk of fuel oil accidentally spilling through the venting system if the tanks are filled above a certain level when the vessel is rolling. Identifying a maximum filling level of these fuel oil tanks, for example, 85%, should be part of a vessel’s heavy weather precautions to mitigate the risk of an oil spill.
4 Heavy weather training: Heavy weather training for deck officers should include instructions focusing on a vessel’s response patterns and the weather impact on a vessel, especially when in ballast condition, along with other weather-affected risks and how these can be mitigated.